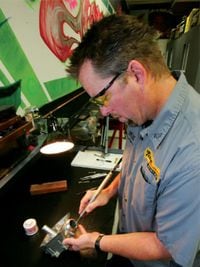
In DR's previous look at a CRF450R head, Tokyo Mods' Ron Wood demonstrated tearing down the top end and prepping it for new valve components. Now we follow Wood's talented hands and pick his brain as he cuts new angles for the valve seats and assembles the valve train like the pro he is. Wood maintains that a correctly assembled valve train is the key to performance and engine longevity. In particular, he insists that the valve guides need to have a snug fit. That means installing new guides and reaming them to the proper size. Naturally, the valve seals are replaced as well. Of all the parts used in this rebuild, the valves are the most expensive. Yes, the little parts do add up, but since they all contribute to the efficiency or life of the valves, it's more prudent in the long run to replace the lot. We are using a Honda head for this story, but the basics are the same for any modern head.As always, these pages do not replace a shop manual but should act as an aid, revealing tips and explanations you won't find in the factory guidebook.
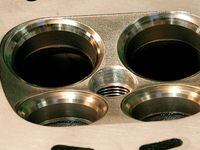
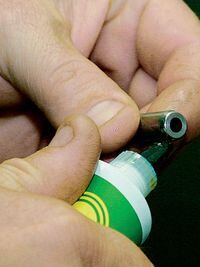
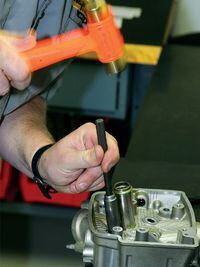
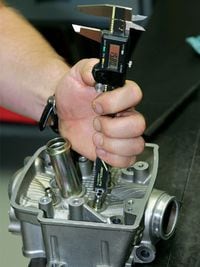
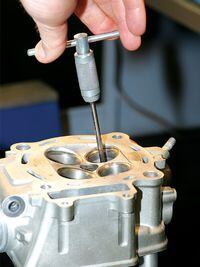
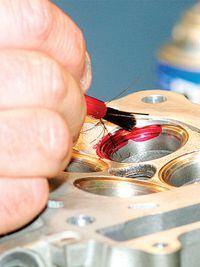
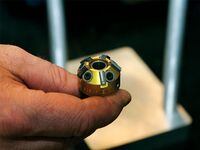
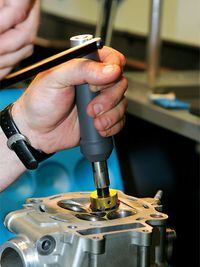
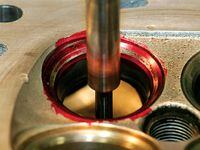
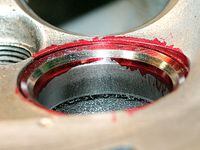
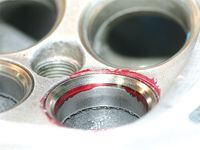
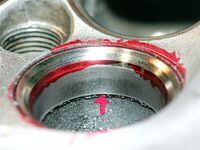
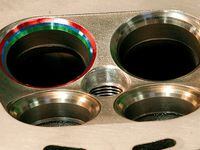
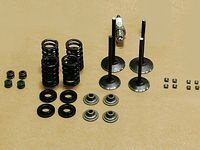
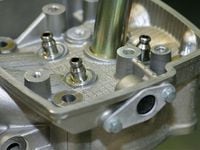
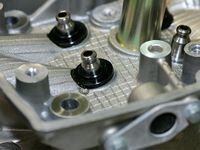
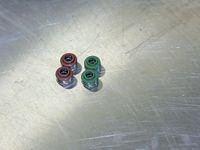
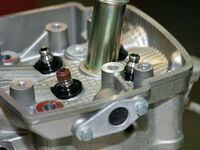
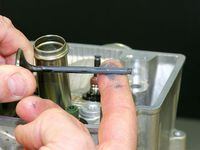
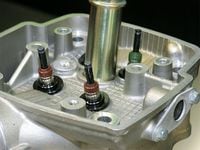
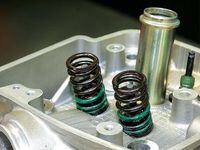
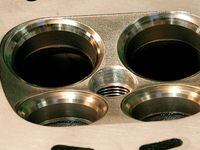
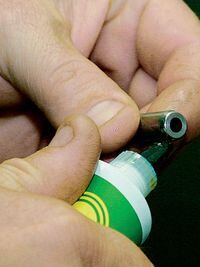
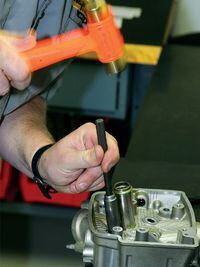
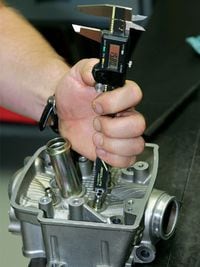
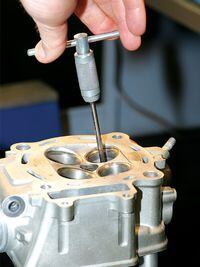
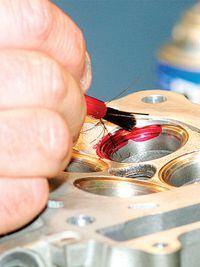
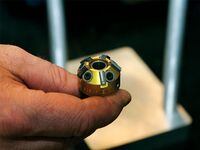
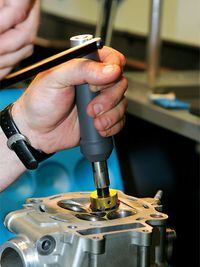
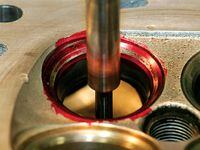
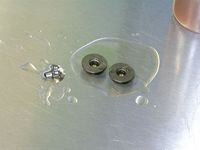
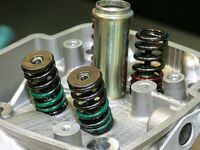
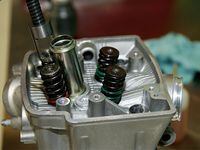
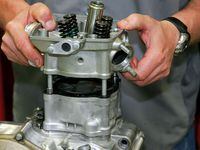
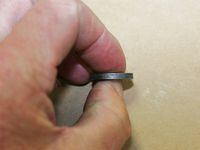
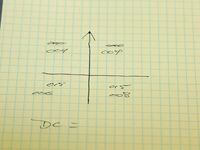
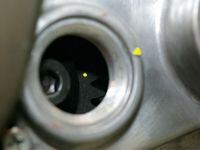
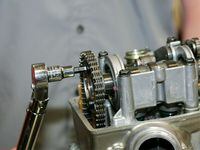
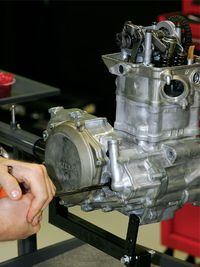
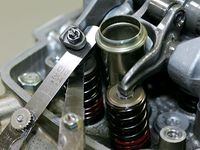
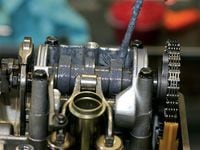
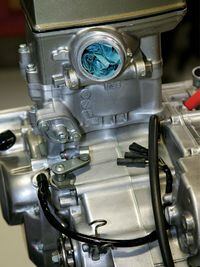
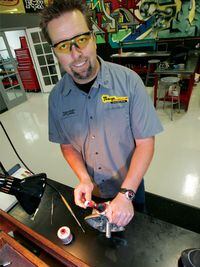
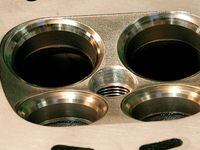
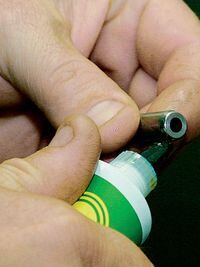
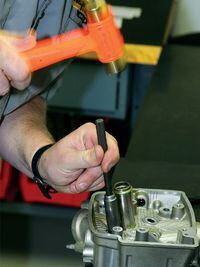
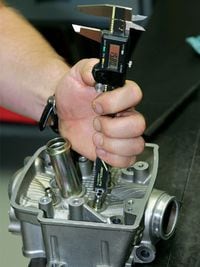
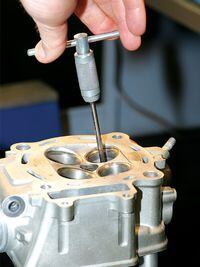
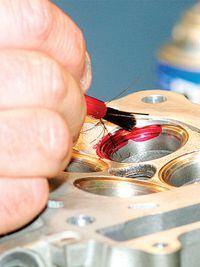
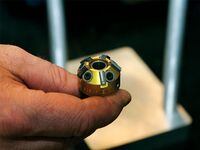
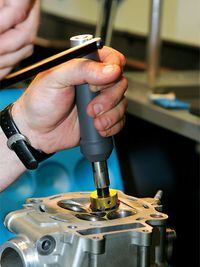
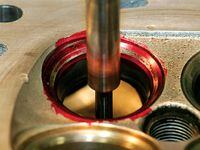